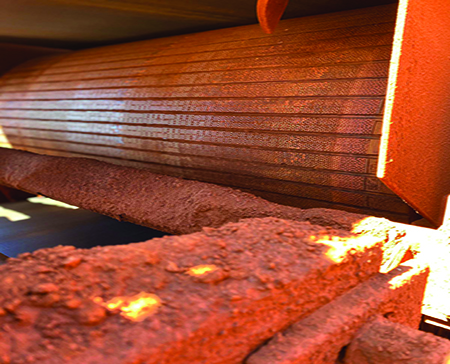
Industry
Iron Ore
Application
Conveying product from the train to ship loader
Product
Flex-Lag® Ceramic Pulley Lagging
Objective
Protect the head pulley
Combat belt slippage
Conveyor Details
1600mm belt width running at 5m/sec, 24 hours, seven days a week
Problem:
As is often the norm, this lagging was applied as part of the site spec. Flex-lag® Ceramic Pulley Lagging was the specified product of choice for this large mine site in the Pilbara, Western Australia. The lagging was specified as a precaution to protect the steel pulley drum and combat belt slippage.
Solution:
The 80% coverage dimple ceramic Flex-Lag was installed in 2001. The lagging boasted the following benefits:
- The moulded ceramic dimples grip the belt’s underside, for positive traction and no slippage
- 80% tile coverage features the highest coefficient of friction available in lagging materials – two to three times the friction of rubber, resulting in lower energy costs
- The cold vulcanisation process makes on-site, in-situ installation fast, simple, and efficient and cheaper than other alternatives
Result:
Although the main goal was to protect the pulley and combat spillage, the most astounding feature of the product was the increased cleaning efficiency of the primary cleaner. The near-perfect condition of the lagging after nearly 20 years in service has allowed the primary belt cleaner to have superior blade-to-belt contact. Another result that was unexpected from the site was the longevity of the lagging given the harsh iron ore material being conveyed. Installed in May 2001, this lagging has been proven to last nearly 20 years; not uncommon for Flex-Lag.