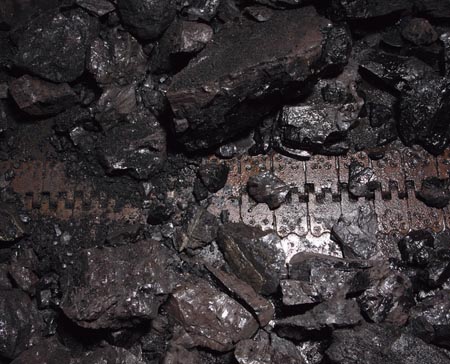
Industry
Coal Transshipment
Application
Mobile Stockyard Stacker/Reclaimers
Product
Flexco® SR™ Rivet Hinged Fasteners
Objective
Avoid downtime and cost of vulcanized belt splicing
Conveyor Detail
Configuration: reversing belts on three mobile stacker/reclaimer booms feed from/to stockyard belts that pass through the mobile units.
Belt Lengths: boom belt is approx. 115' (35 m) between end pulleys; stockyard belts approx. 3050' (930 m) between end pulleys.
Belting: stockyard 63" (1600 mm) wide; stacker boom 55" (1400 mm) wide, 19/32" (15 mm)-thick, 5-ply, all-rubber Type 1250.
Typical Load: inbound/stacking up to 3,000 tph; reclaiming/outbound up to 2,000 tph.
Typical Speed: 9'10" (3 m)/sec.
Problem
Although plied-rubber belts can be mechanically fastened, the maintenance manager preferred vulcanizing, expecting it to most closely match the strength of the belt ... but vulcanizing took 24 hours or more for proper installation including waiting time, bringing in cranes, de-rigging and re-rigging the conveyor ... at a total cost of about $4,500/splice. Idling a stacker for one day could cost another $12,000 in lost income, and could invoke up to $25,000 in contractual penalties for delaying ship departure. Increased traffic resulting in three-shift, round-the-clock operation put high priority on finding a faster, cheaper way to get broken belts back into service.
Solution
Seeing widespread use of Flexco® SR™ Rivet Hinged fasteners in underground mining, quarrying, and tunneling gave the manager confidence to try it here. This rugged steel fastener consists of 1-1/2" (38 mm)-wide top and bottom plates joined at one end by two wide hinge loops. Each pair of plates sandwiches the belt end and is secured with a staggered pattern of five rivets. Plate segments are installed side-by-side across both belt ends, in continuous strips that assure proper spacing and alignment. A special installation tool locks the strips and belt ends in proper position while selfsetting rivets are hammered through the plates and belting. Preassembled with breakaway pilot nails, the rivets slip between rather than slice through load-bearing carcass fibers. An anvil plate in the installation tool captures the pilot nails beneath the splice, then the pilot nail head works with the anvil plate to peen the rivets automatically, releasing the pilot nails in the process. Plates are compressed into the belt cover with a tight broad grip. Flexco MSRT tooling allows all 5 rivets in each plate to be driven simultaneously through pre-loaded guide blocks, greatly speeding the process.
Result
The speed advantage of SR was demonstrated when a boom conveyor suddenly tore as a result of edge damage during a ship unloading. On-site workers cut out the damaged section nearly 10’ (3 m) long and spliced in an insert with SR at both ends, completing the job in less than two hours at a total cost of less than $400. Hinged SR splices brought another benefit as well. Idlers and impact bars under the boom/stockyard belt transfers need replacing and drive pulleys need re-lagging on regular schedules, requiring belts to be parted and moved away. With SR splicing, belts are easily opened up and rejoined by pulling and replacing the hinge pin, saving the previous time and expense of vulcanizing the belt back together again. Now all boom belts are routinely installed with SR, and this handy splice is trusted for emergency repairs on the stockyard belts as well.
Shop Flexco Fasteners