Industry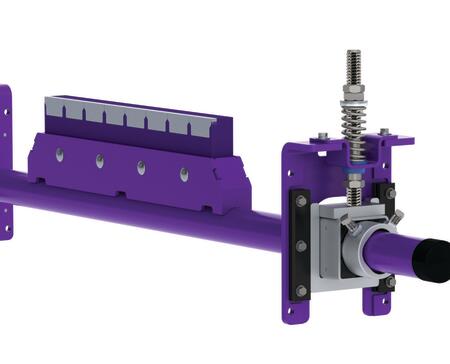
Open Pit-Hard Rock Mining
Application
Carryback reduction and belt cleaning
Product
CBS Continuous Blade Secondary Cleaner
Objective
Decrease maintenance needs, improve belt tracking, increase site safety
An iron ore mine in Australia was experiencing extreme amounts of carryback on an incline conveyor, causing spillage along the entire conveyor line. Additionally, the carryback would trigger belt misalignment at the centrally-located drive causing premature wear to the conveyor belt edges, idlers, and pulley lagging. A significant amount of time and money was spent cleaning up the sticky, wet product from the structure and the ground beneath the conveyor. During scheduled six-week shutdowns, the site would require one vacuum truck and operators, one skid steer and an operator, and two individuals manually shovelling carryback from the bottom of the conveyor bin and adjacent systems. This would typically take two 12-hour shifts to complete.
In addition, an average of 15 return rollers were replaced every six weeks during the shutdown. Given that this is an incline conveyor, the replacement necessitates the use of an Elevated Work Platform (EWP), which introduces a range of safety hazards. This task typically requires approximately five hours to complete, including the setup of exclusion zones, obtaining permits, and locating the EWP. To execute the task safely and efficiently, it mandates the involvement of four technicians and one scaffolder, contributing to additional labour costs.
The carryback was not only creating significant disruptions to their operation and productivity but also posed a major safety hazard for personnel walking around the site. Given the wet, sticky nature of the conveyed material and the substantial volume of carryback, it presented a considerable slip and trip risk, further exacerbating safety concerns.
The site contracted a Flexco distributor who invited their local Flexco Territory Manager to inspect the problem. They found that the previous two cleaners (secondary and tertiary) were not able to tackle the carryback as the tensioners were behind a guard, meaning maintenance personnel were unable to tension the cleaners during the 24/7 operation. This meant that they had to wait until scheduled maintenance days every six weeks to safely adjust the cleaners.
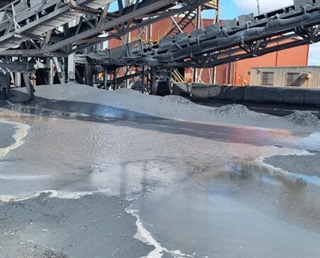
Before
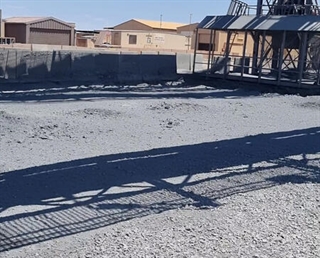
After
FINDING THE RIGHT SOLUTION
After measuring and reviewing drawings, Flexco and their distributor proposed to replace the two existing belt cleaners with a CBS Continuous Blade Secondary Belt Cleaner with a flat blade in the secondary position and a MDWS Dry Wipe Heavy-Duty Secondary Belt Cleaner in the tertiary position. Both belt cleaners are known for providing excellent cleaning efficiency in wet and sticky applications. A Live-Shaft Hold- Down Roller was installed in between the two cleaners to eliminate belt flap and stabilise the belt.
These were paired with an EZ-Air Tension Kit (EZK) to provide constant air pressure for each cleaner. The EZK has been designed to adjust the blade pressure in the easiest and safest way possible. The control box is accessible outside the guard, meaning maintenance personnel can safely access and check the tension whilst the conveyor is in operation. Plus, to tension the cleaner, personnel only need a battery-rechargeable handheld compressor, which reduces the need to carry multiple tools and heavy tool bags to the top of the conveyor.
To further assist with monitoring the belt cleaners, Flexco Elevate® IoT was installed on both belt cleaners. This revolutionary technology is designed to remotely monitor belt cleaners and belt health in real-time, using machine learning insights to prevent issues like carryback. Once the i3 device is installed on any Flexco belt cleaner pole, the insights are immediately transferred to the Elevate dashboard. This information is then combined with maintenance data logged by the site’s team on the mobile app, providing predictive data-driven insights that can be accessed directly from the dashboard. This allows for remote monitoring of the productivity of belt cleaners and notifications when they require attention.
The distributor's mechanical crew, under the supervision of Ian Kennedy, Territory Manager from Flexco, completed the removal of the existing belt cleaners and installation of new solutions.
The collaboration between Flexco, the distributor, and the client led to the successful development of an effective, tailored solution to their carryback challenges. Through ongoing discussions, an initial concept was quickly refined into a practical design. On the day of installation, Flexco provided on-site support, offering valuable expertise that ensured a smooth and efficient implementation.
THE CLEANEST THE AREA HAS BEEN IN FIVE YEARS: RESULTS REVEALED
After the products were installed, the belt mistracking and carryback issues were immediately resolved. There is no longer wet carryback below the conveyor on the ground, which has eliminated the safety issues previously created. The belt is now tracking central to the structure and rapid component wear on the idlers and lagging has declined.
The conveyor was able to run consistently for the entire six-week run time due to the enhanced cleaning efficiency created by the constant blade-to-belt contact provided by the cleaner and new tensioning system.
During the next shutdown following the installation of the products, only three return rollers required replacement, a task completed in just 1.5 hours. This notable reductionin manual labour not only greatly enhances the safety of the technicians, but also substantially decreases labour costs for the site.
The site found that 95% of the maintenance tasks caused by carryback in this area, including shovelling carryback and replacing idlers, have now been redeployed to other areas on the site. This allows their operation team to concentrate on other troublesome areas within the plant and significantly reduces their clean-up costs.
Being one of Flexco's latest belt cleaning solutions, this was the first time the Distributor installed a CBS cleaner, and it exceeded their expectations. It was installed on an old, worn belt with impact damage and skirt wear on the top cover and was able to effectively clean the belt despite the belt condition.
With the success of the combination of two belt cleaners and tensioning systems, the Flexco distributor and Flexco are now in conversations with the site to add additional EZK systems, plus they are considering upgrading more conveyors to the CBS belt cleaner.