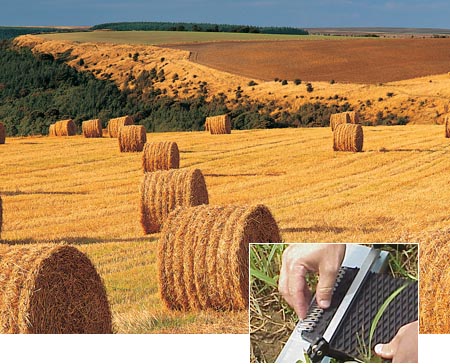
Industry
Agriculture/Hay baling
Application
Round hay baler rolling belts
Product
Alligator® Rivet Fasteners
Objective
Minimize field downtime and splice replacement costs
Conveyor Detail
Belting: 7" (203 mm) wide, plied rubber belt, 3/16" (4.8 mm) thick with diamond-pattern top cover
Belt Roller Minimum Diameter: 3-1/2" (89 mm)
Typical Load: 4' (1.2 m) wide bales grow to 5' (1.5 m) high, with 10-11% moisture can weigh 1,000 to 2,000 lbs. (453-907 kg)
Problem
Working his own 150 acres, while providing contract baling for neighboring growers can push this Texas farmer’s annual bale output up to 7,000 bales per year. This one-man operation typically runs seven days a week from May until autumn’s first frost, placing a high priority on avoiding breakdowns in the field. The belt lacing he had always used, made of thin-wire loops connected by a hinge pin, needed constant checks to avoid sudden failures. The hinge pin could wear through the ends of the hook loops and allow them to open, or the loops could cut into the pin until it broke apart, or the hook undersides could wear through from passing over the machine’s rollers. If a belt broke while a bale was forming, the bale could roll the belt up inside, forcing a stop to unload the bale and dig the belt out. A few more hours would be lost driving the belt back to the shop for re-splicing with a special lacing machine. The only alternative was to carry pre-laced spare belts that cost about $300 each.
Solution
Alligator® Rivet baler belt fasteners brought relief with long-wearing plate segments made of 3/32" (2 mm)-thick stainless steel instead of thin wires, wider hinge loops, and hardened spring stainless connecting pins twice as thick as those used with hook splicing. Each plate segment attaches to the belt with a rivet, placed 5/16" (7 mm) in from the edge of the splice to prevent belt fatigue due to flexing along the points of attachment. Splices are installed with a hammer and small applicator tool, easily carried and used in the field if necessary. Fastener segments are joined along their bottom plates, forming strips sized for standard belt widths. Strips are locked into the applicator tool, the belt end is inserted into the strip and butted against built-in belt stops, then a clamp on the tool secures the assembly while self-setting rivets are hammered through the splice plates and belting.
Result
In contrast with his previous wire hook splicing, which at best rolled about 5,000 bales before needing replacement and often didn’t last a full season, this farmer reported that his Alligator Rivet Fasteners were entering their third season still showing very little wear. He also credited Alligator’s wider loops and thicker hinge pin with extending pin life to about three months, in sharp contrast to the three-week life of the wire-hook hinge pins. Although the riveted splice is more expensive, he notes that over the life of the belts, he “gets that back and then some” by not having to re-splice nearly as often.