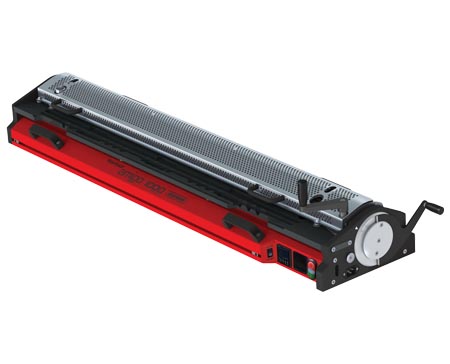
Industry
Baking
Application
Conveying baked crackers
Product
Novitool® Amigo™ Splice Press
Objective
Save time
Produce consistent splices
Operator safety
Conveyor Detail
Multiple monolithic belt types
Problem:
A major contract bakery manufacturer was unhappy with the quality and consistency of the splices on their belt conveyor line for a number of reasons.
First was the issue of downtime. The conveyor lines had to be joined together via endless splicing, and unfortunately the butt splicing tools that the maintenance team used took 30 minutes to complete, including preheat time. Their second concern involved splice performance. The splices that were being installed were inconsistent, leading to premature failures, sometimes at inopportune times. Since different people with various levels of experience were splicing the belts from shift to shift, the splices were oftentimes inconsistent and pinholes were present. The craftsmanship of each operator made a difference when using the butt splicing tools.
Lastly, their outdated splicing technology required installation processes that were difficult, inefficient, and worst of all, dangerous. The customer had two different splicing systems that they were using based on the belt type. The first type uses a heater wand and a template fixture. The heater wand is unprotected and reaches an extremely dangerous temperature. This causes an unsafe work environment for the operator and bystanders. The second system is also concerning, as it requires the operator to bevel cut the belt ends with a rotor and then weld a urethane rod between the two belt ends using an unshielded heat gun.
Solution:
After watching a demonstration of the Novitool® Amigo™, a splice press specifically made to join monolithic belts, the maintenance team was amazed with the results and decided to use it on some upcoming repairs. The maintenance crew brought the Amigo directly to the conveyor for the splice install and found that it provided them with benefits with each process step. The first step was cutting the belt ends to the correct length. They started by choosing the template for the belt they were using. The Amigo has 10 templates from which to select, covering the majority of the monolithic belts on the market. The customer actually has three different types of belts within their facility, making the Amigo a versatile splicing tool for their purposes. Once the proper template was chosen and the belt securely clamped in place, the integrated cutter provided a safe, quick, and efficient method to create an accurate cut.
The next step in the process involved removing moisture from the belt ends prior to splicing using the preheat function. With their current process, this moisture would result in undesired pinholes in the finished splice, which was not a problem with the Amigo.
And the benefits continued in the final step – the actual splicing. The heat source used to make the belt ends molten never comes in contact with the belt ends and, more importantly, never comes in contact with the operator. Also, the heat shield must be in the proper position to function, thus protecting the operator during the splicing procedure. By never coming in contact with the belt ends, the material is not disrupted during the splicing process, producing an optimal finished splice. The actual splicing time averaged to just over one minute. Another safety feature is evident when the splice is complete. Once finished, the heating element is simultaneously moved into the storage position, free from the possibility of burning the operator.
Result:
The first belt they spliced only required 300 seconds to preheat and 55 seconds to splice, for a total time of less than six minutes. The settings for the second belt were 600 seconds of preheat, followed by an 80-second dwell time for the splicing. Both splices required far less time than their existing splice tools did. The bakery now has a single splicing tool that is capable of splicing all the different monolithic belts in their facility with speed, accuracy, and safety.