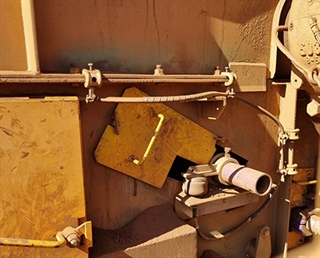
Industry
Iron Ore
Application
Shuttle Conveyor Belt
Product
Portable AirTensioner (PAT) system with an H-Type® Primary Cleaner
Objective
Reduce carryback, Improve maintenance expenditures
Maximise safety
Conveyor Details
1800mm wide, 5m/sec
Problem:
For belt cleaners to be effective, they must maintain constant blade-to-belt pressure, achievable with either a manual or automatic tensioning system. However, operations must decide on the right tensioner for their application and maintenance resources as improper tensioning can lead to blade chatter, reduced cleaner efficiency and excessive carryback.
An Australian iron ore mine in the Pilbara region was utilising a spring tensioning system on one of their shuttle conveyors. Spring tensioners can be manually adjusted by measuring and adjusting the tension as needed until your next scheduled maintenance check. Unfortunately, in this case, the spring was rarely adjusted or monitored as it was in a confined location, resulting in carryback outside the chute as well as material build-up on the rollers. Ultimately, the site’s latter option was to halt production and move the shuttle conveyor into a maintenance position each fortnight, which would involve an electrician to carry out the isolation, operators needing to be present, permits to be authorised, workplace inspections to be completed by supervisors, along with the mine control team being notified. This task not only required 3-4 experienced technical staff, but it would also result in 2-3 hours of lost production.
Solution:
After speaking to a Flexco representative about their challenges, Flexco was able to propose a solution that did not require isolating the shuttle conveyor and the additional costs that come with that process – A Portable Air Tension (PAT) System. This type of tensioning system is most effective for confined areas such as shuttles, as this type of side assembly will maintain tension on its own and does not need to be checked regularly. The PAT system was also paired with Flexco’s H-Type® Primary Belt Cleaner to create the ultimate cleaning system that required minimal maintenance.
Result:
The PAT system was able to provide the optimum blade-to-belt tension throughout the running period of 14-16 weeks and significantly reduced carryback and product build-up along the conveyor. The PAT system eliminated the need for isolating the conveyor, preventing a 2–3-hour production loss and the need for 3-4 labour staff fortnightly. Now one technician is required to perform external visual inspections of the pressure gauge with no tooling required to perform tensioner adjustments. This greatly reduces the safety hazards involved in manual inspections and eliminates technician error. Based on the success and performance of this PAT system, the site has now planned to installmultiple PAT systems across their shuttle conveyors at their operation.