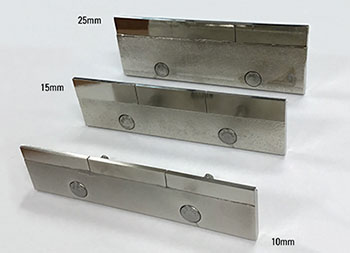 |
Flexco Tungsten Tip Size Comparison |
High throughput in iron ore mines coupled with abrasive material means that your belt cleaners are the piece of equipment on your belt line that see the worst of your belt and the worst of your material. So optimising your cleaners for a longer shut down cycle should always be a primary focus.
Customer Driven Innovation
The average tungsten carbide cleaner tip is 10-15mm long. This is an optimal length when mining resources such as metallurgical and thermal coal – but not for iron ore.
Knowing this information and the need for an extended tip length in the market, Flexco set to work on creating a new tungsten tip to test in collaboration with a large mining conglomerate in Western Australia. Using the highest possible grade of tungsten carbide, Flexco created, manufactured and begun to test a 25mm secondary cleaner tip to complement Flexco’s existing 25mm primary cleaner tip - which would eventually prove to last a full 20+ week shutdown period.
Results that Matter
I was lucky enough to instigate and manage this trial on site with great results. Thanks to these new tips, this particular site moved from a standard shut down cycle of 12 weeks to what they called a 10/20 week cycle. The idea behind this was to carry out minor works during the 10 week shut down, and leave other major works such as cleaner tip change out for a 20 week shutdown. With the help of Flexco’s improved tungsten tip length, the site was able to successfully last a full 20 week cycle without conducting general works apart from routine tensions.
Apart from limiting downtime, what did this mean for the site?
Savings – in both time and money.
Before the launch of Flexco’s tungsten tip innovation – the site was purchasing 15mm tips every 12 weeks, equating to about four sets per year, per conveyor. With the help of Flexco’s improved tungsten tip length, the site was able to successfully last a full 20 week cycle without conducting general work. This equates to a 20% cost reduction per annum in the amount of downtime and labour the site paid for on just one conveyor.
The site also saved the time it took to replace existing tips during shutdowns. This saves about an hour for each cleaner on the belt. With some conveyors having in excess of four cleaners, this amounts to about eight hours per conveyor, per year. This is time that can be better allocated to other productivity boosting projects on site.
Due to the outstanding trial results – the iron ore site has specified the 25mm tungsten tips for all cleaners on conveyors part of the 10/20 week shut down strategies.
Looking for ways to reach your goals?
Flexco understands that iron ore mines need to get more material to the ports than ever before. So ensuring your belt conveyor systems are working at their absolute optimum is a necessity. That’s why we offer free belt conveyor assessments, performed by your local Flexco expert. To register for a free Flexco audit, click here.
Authored by: Jason Coe, West Coast Heavy-Duty Specialist
Coe joined Flexco in 2012. Prior to joining Flexco, Jason worked in the Western Australian mining industry for more than 10 years as a belt conveyor system maintenance supervisor. He has significant knowledge of belt conveyor system cleaning systems as a result of his eight years as a cleaner technician. Coe holds various trade qualifications.