Not too long ago I wrote a blog about the different modes of roller failure – abrasion and corrosion, seal design, and end disk failure. The next biggest question I get asked as a conveyor roller expert is, “How do I select the right rollers for my belt conveyor application?”
Belt rollers greatly impact the productivity of a system, and that means they should be carefully selected and matched to each application for maximum longevity and performance.
Today we’ll explore the most important factors to consider when selecting the right roller for your application: The life and weight of the roll, power consumption, noise generation, and corrosion-resistance.
Longevity: How long does a roller last?
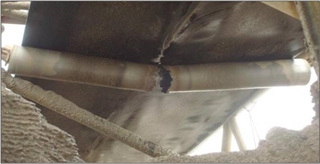 |
A premature steel roller failure. |
Most rollers are selected on the basis of theoretical bearing life calculations; this helps to determine which rollers are recommended based mainly on load and speed. However, roller life is determined by many factors including;
- Seals
- Bearings
- Shell thickness
- Belt speed
- Lump size/material density
- Maintenance
- Environment
- Temperature
- Idler design
Additionally, seal design is key to the success of the bearing and to the success of a roller. A seal design that is resistant to moisture and other fines protects the roller from contamination and internal corrosion. It is estimated that 43% of bearing failures come from moisture and other contaminants. One way to prevent this is by opting for a roller with a quality centrifugal flinger seal, offering up to nine times more centrifugal force, to help “spin out” fines, water, and other contaminants.
Weight: Is roller weight an issue?
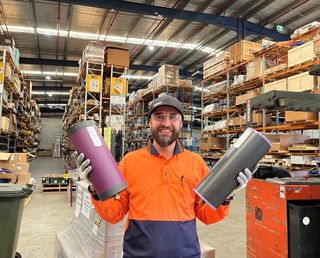 |
Worker carrying a lightweight CoreTech™ Nylon and HDPE composite rollers. |
The answer is simple. Yes. Weight is always a concern when it comes to the safety of your employees. It often takes only a single reportable injury at your workplace to raise your workers’ compensation insurance premiums, lower your productivity, increase your absenteeism, and possibly increase your legal costs fighting an injury suit.
Traditionally, conveyor rollers have been constructed from steel, and the heavier the application, the heavier the roller. A single 1800mm roller can weigh up to 45 kg, making the roller difficult to carry and install.
Opting for a polymer-based roller, weighing up to 40% less than steel, is a wise choice. With a lighter option, you not only have less of a chance of a workplace back injury, but increased productivity as product performance can also be a factor when the rolls are heavier. Routine roll maintenance duties may be neglected because the rolls are large and cumbersome to replace.
Power: How do rollers affect my power consumption?
Belt conveyor systems often operate 24/7, so making sure your rollers are running as efficiently as possible can only add dollars to your bottom line. While the power to rotate a single roller is small, it accumulates along the length of a conveyor.
Two factors contribute to the energy consumption required to operate a large number of rollers on a system. The first is breakaway energy – the power required to get the conveyor started (as much as 13% of your power). The second is the running friction – a substantial amount of energy is required to keep the rollers running.
When it comes to energy savings, engineered Nylon or HDPE rollers are a smart choice. They have lower running friction values, which, depending on the application, can decrease power bills by up to 30% per annum. Installing rollers with non-contact seals is also wise if you are looking to save money on power because they require less breakaway energy and reduced friction numbers.
Noise: Is noise an issue for your operation?
It is surprising how much of the noise from bulk material handling systems is generated by rollers. Heavy material loads, friction between the belt and rollers, and splices reverberating over the rollers can affect the sound produced by your conveyor systems.
In many countries, local jurisdictions and municipalities have their own laws about noise regulations, and heavy fines can be levied when noise exceeds allowable levels.
If your operation isn’t located near a residential area or within a jurisdiction that has stated noise ordinances, you’re safe from a governmental point of view, however, how safe are your workers? Continuous exposure to elevated noise levels can be dangerous for employees.
Corrosion: How does corrosion-affect rollers?
One of the main causes of premature roller failure is corrosion, externally or internally. Since environment, temperature, and the type of material being conveyed can’t be changed, many people just write off corrosion as an inevitable occurrence. However, that doesn’t have to be the case. Both the material the roller is constructed from, as well as the seal design that protects the bearing, can make a huge impact on the life of the roller.
Metal can rust, corrode, and scale. Polymers are more resistant to corrosion than metal. Rollers that match the ratings of steel are now available in polymers such as engineered Nylon and HDPE. These materials are resistant to corrosion from chemicals, salt, and moisture. Steel rollers can fall victim to several environmental factors. When exposed to moisture, nylon actually gains toughness while virtually eliminating the risk of premature failure due to surface corrosion.
A verified solution
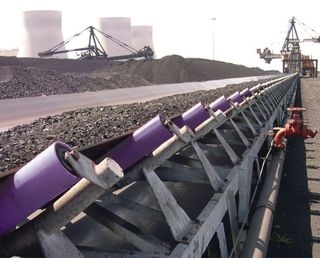 |
Flexco CoreTech™ composite rollers. |
CoreTech™ Composite Rollers offer the absolute best combination of structural strength coupled with the requirements of mining, which include corrosion resistance, excellent abrasion resistance, and very low surface friction. Available in both engineered Nylon and HDPE, CoreTech rollers are approximately 40-50% lighter than equivalent steel rolls, requiring only one individual to lift, carry, and place the roller. CoreTech rollers utilise less energy to create rotation than standard steel rollers. They also maintain a given RPM. The estimated noise contribution of the CoreTech rollers was +/- 10 dB below the noise contribution of the steel rollers, which means the CoreTech roller emissions were a tenth of the sound energy emission of the steel rollers.
If you interested in switching your steel rollers to CoreTech composite rollers, get an obligation-free quote here or chat to an expert via marketingau@flexco.com.
Authored by: Jayden Baker, West-Coast Regional Manager
Baker began working at Flexco in 2014 as a Territory Manager in Western Australia, before taking on the management role for the entire West Coast of Australia in addition to his current duties. He has worked in mining for 15 years, specialising in machine and automation safety. Baker holds qualifications in management, boiler making, and mechanical fitting.