When it comes time for conveyor belt repair, the most important part of the process is often the most overlooked. Along with squaring the belt before cutting, skiving the belt is an area that is often missing in the repair process.
Skiving a belt removes a portion of the belt top cover to simplify fastener installation. All the strength of the belt is actually found in the belt carcass, so removing the cover does not weaken the belt. When you skive a belt, you replace the protective cover with the belt fasteners, which produces a stronger grip on the belt carcass.
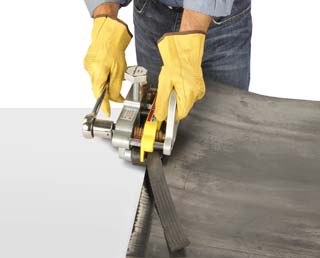
When skiving, leave 1/16” (1.5mm) of the belt cover in place
to provide protection from elements such as water and sun.
So why should you skive your belt?
1. Skiving helps you achieve a lower mechanical belt fastener profile
Since skiving a belt removes the top layer from the belt, it leaves room for the fasteners to lie even with or below the rest of the belt surface. This feature reduces the chance of the fasteners interfering with any of the belt components or conveyor structure.
2. Skiving a belt increases belt cleaner life
When a belt is skived, and belt cleaners and other conveyor components are able to work on a smooth surface without seeing interference from the belt fasteners, your system runs a lot more efficiently. A skived belt creates a compatible surface for cleaners and increases cleaner blade and fastener life.
3. Skiving the belt improves fastener wear when used with skirting
A skived belt also reduces wear and tear on the skirting and fasteners, resulting in prolonged operation and reduced maintenance. Placing the top of the fasteners beneath the lower edge of the skirt rubber eliminates excessive wear on both the skirting and fasteners.
4. Skiving increases splice life
Skiving a belt will ensure longer splice life by achieving a lower profile, which prevents excess wear and tear on the fasteners and extends the life of the belt.
5. Skiving increases the strength of the splice
When using a bolt solid plate type fastener, the skiver removes the top rubber layer from the belt to ensure that the teeth of the fastener are properly engaged in the carcass. By placing the top and bottom fastener plates closer together, a stronger belt splice is achieved.
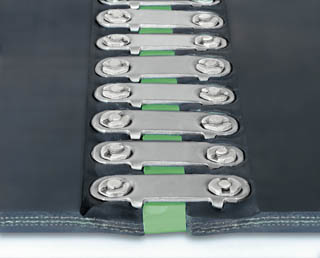
A properly skived belt allows the fasteners to sit lower, reducing the wear and
tear on them and on belt conveyor components they may come into contact with.
When Not to Skive
These are all great reasons to grab a belt skiver and get to work, but is there ever a time when it would be wise to put the skiver away? Absolutely. Skiving is not recommended for belts with thin or worn top covers because the chances of you cutting into the carcass and weakening the belt is too great.
Also, fastener selection matters in the skiving process. In fact, skiving the belt may adversely affect the splice if the wrong sized fastener is used because your choice of a fastener relies heavily on the belt thickness.
Finally, never, ever use time as an excuse to properly skive your belt. While skipping that step on the front end of the maintenance process may seem like a good idea, it will inevitably result in additional downtime down the road.
For more information on proper belt skiving, check out our FSK2 Belt Skiver video.
Authored by: Aaron Rosso, Senior Product Manager
Rosso is responsible for managing the heavy-duty mechanical belt fastener program globally for Flexco, including the program vision and strategy, product development plan, product line portfolio, promotion, PR and communications, pricing, and profitability. Rosso graduated from Western Michigan University with a bachelor’s degree in Finance and received his master’s degree in business administration from the Kellogg School of Management at Northwestern University with a concentration in Marketing and Strategy.