Choosing the proper mechanical belt fastener is one of the most important steps in splicing a belt. Using an inappropriate fastener can lead to premature splice wear or even a catastrophic failure of the belt and splice, both of which lead to increased conveyor downtime, as well as safety concerns.
That’s why the selection of the correct mechanical belt fastener is crucial to the system. The correct fastener will not only decrease your downtime; it will also increase your operation’s productivity.
So how do you figure out what mechanical fasteners will work better on your belts? Well, while there are many factors to take into consideration, proper fastener selection relies heavily on what is often called “the big three” – belt rating/tension, belt thickness, and pulley diameters.
Flexco’s Heavy Duty Mechanical Belt Fastener Selection Calculator helps you take “the big three” into account when choosing the right fastener for your application. Read on for info on what numbers you’ll need to select your fastener.
Examining belt rating/tension
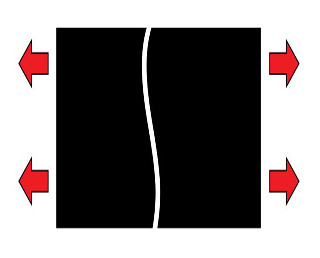 |
Care should be taken not to operate the belting or fasteners beyond their recommended ratings. |
Each belt comes with a tension rating from the belt manufacturer, which is a measurement of the tension required to overcome the friction of the conveyor components. The conveyor components considered in this rating consist of the weight of the material being conveyed; the angle of the belt; and resistance from idlers, skirt board, and other system components. When it comes to belt ratings, they can vary, depending on your location.
In certain areas of the world each belt is rated to its operating strength (after safety factors) and is classified in terms of Pounds Per Inch of Width (P.I.W.) Similarly, each mechanical fastener is also rated in terms of P.I.W.
In other areas, belts are rated to its overall belt strength (before safety factors) and are classified in terms of Kilonewtons Per Meter (kN/m). Because of this, each mechanical fastener is also rated in terms of kN/m.
Regardless of whether you rate your belt by kilonewtons or pounds, it is important that both the belt and the fasteners are operated within the range of their capabilities or the splice may fail prematurely.
Determining conveyor belt thickness – the right way
Determining conveyor belt thickness seems like a simple enough thing. You knew the thickness when you bought the belt, so that measurement is the easiest of all three, right? Maybe. Maybe not. If your belt is new, you can feel confident that you have the correct measurement, but if it isn’t, you have to take some factors into consideration.
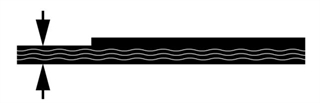 |
Always measure belt thickness after a portion of the belt cover has been removed. |
First of all, you can’t calculate belt thickness by measuring the belt thickness at any point. The key is to measure it at the point where the splice will be installed. As the belt runs, it comes into contact with any number of items – pulleys, idlers, lagging, and the material that is being conveyed. Contact with these items wears both the top and bottom cover of the belt. This is why it is important to know the belt thickness in the area where the splicing will take place since belts generally don’t wear evenly.
The next step in determining the thickness is whether or not you will be skiving the belt. Skiving the belt enables you to countersink the fasteners into the belt by removing some of the top cover of the belt. This allows better interaction with other components of the conveyor without affecting the strength of the belt. If you have a top cover of at least 3/16” (4.5 mm), it is recommended that you skive the belt. While skive depth can range from 1/16” (1.5 mm) to 3/8” (10 mm), the average skive is 1/8” (3 mm), which accounts for the thickness of the fastener. Make sure you keep this depth in mind when determining the thickness of the belt because you will need to measure the belt and then subtract the amount of belt that you intend to skive.
Each fastener is engineered to handle a different range of belt thicknesses and it is important that you pick the fastener that is suited to that range. Otherwise, premature belt wear and splice failure become real possibilities with your system.
How pulley diameter factors into your choice
The final factor to take into consideration when choosing a fastener is pulley diameter. The question here is: which pulley? Well, you can start by taking note of all of the pulley diameters on your system where the belt wraps at least 90 degrees. Choose the smallest pulley that wraps 90 degrees or more. If you have a self-cleaning, wing-type pulley, factor in a 25% larger diameter dimension.
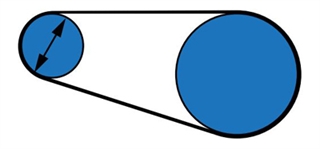 |
Measure the diameter of the smallest pulley in your drive. |
Pulley diameter is an integral part of deciding between the two different types of fasteners – solid plate and hinged style. Hinged style fasteners, for example, are more popular for smaller pulley diameters, because of their ability to bend around a tighter turn in the system. When either style is appropriate for your belt and pulleys, solid plate styles are preferred for longer life and to prevent sifting. Hinged fasteners are preferred on smaller diameter pulleys, portable conveyors, and any situation where the belt length may be adjusted.
Using your calculations
If you take all these factors into consideration, then you have all the info you need to find the right fastener for your system. Plug them into the Heavy Duty Mechanical Belt Fastener Selection Calculator to choose the correct style of fastener. From there, here to our Mechanical Belt Fastenings Systems page to learn more about the fastener.
If you’re not sure if you’ve made the right fastener decision, we’d advise you to schedule an assessment with your local Flexco expert. Click here to have a member of Team Flexco come out to your site and assess your system and make recommendations to optimize the productivity of your operation.
Authored by: Russ Heintz, Training and Technical Specialist
Russ Heintz has been with Flexco since 1995, working in various roles within the company before becoming Training and Technical Specialist. In this role, Heintz focuses on the efficiency of our products through in-house and field testing. Heintz also regularly conducts classroom and hands-on, internal or on-site training with Flexco employees, distributors, and customers.