It’s no secret that a conveyor belt running smoothly and consistently is a major productivity boost for your conveyor system. If you have material caked on your belt, rollers, or pretty much every component on your system, then you have a problem with material carryback. This is a problem seen regularly in food processing, pharmaceutical, recycling, and other light-duty belting applications.
Your product carryback is actually affecting every part of your operation, resulting in decreased product output, lost productivity because of maintenance and repairs, and a dwindling bottom line. Add in the cost of having your maintenance team clear the excess scrap, along with trying to clean and sanitize your system, and your pocketbook is shrinking.
In the past, it seemed to be inevitable – a cost of doing business. But when you’re trying to trim your budget, every ounce of wasted product and every shut down for repair or replacement is an area of opportunity. It’s time to do something about it. But what can you do to keep your materials on the belt throughout the production process? Install an efficient belt cleaner.
Homemade Cleaners
Since your maintenance team knows the ins and outs of your conveyor, it’s natural to think that they can develop a cleaner that will conform perfectly to your system. And oftentimes, they do just that. Scrap conveyor belting, spare pieces of plastic, and even stainless steel are used to create devices that “scrape” the belt. While this is an inexpensive design that can remove some carryback, it is not always the best for the health of your belt or product removal from the belt, and it is far from sanitary.
Proper tensioning is critical for efficient and effective cleaning. Many homemade scrapers apply too much pressure and cause damage to the belt or splice, while others do not apply enough pressure, allowing carryback. Worse still, some systems have variations in the belt or pulley that render a rigid tensioning system ineffective.
Without an appropriate tensioning system, the cleaners are not providing constant blade-to-belt contact and product is getting past the homemade cleaner, causing it to stick to the belt and conveyor components.
Also, many homemade cleaners and their hardware or mounting systems are not made of food grade materials and have crevices that can actually harbor bacteria and other potential contaminants. In addition, the complexity of their construction can make cleaning and sanitizing a difficult task.
This real life result explains how a homemade belt cleaner at a glass manufacturer ended up doing more harm than good. The manufacturer was experiencing serious problems on its recycling belt and the homemade belt cleaner that was being used was not effectively cleaning off the belt.
The result was glass embedding in the belt, which caused it to crack on the edges and fail. Additionally, the design of the homemade cleaner – a piece of UHMW bolted on to the structure – was actually doing more harm to the belt by digging into it. Because there was no “give” to the blade, the belt was being further damaged and the blade was wearing at an alarming rate, meaning more frequent maintenance.
The plant was able to increase belt life and decrease time spent on maintenance by installing an engineered cleaner. You can read more about this real life story here.
Engineered Cleaners
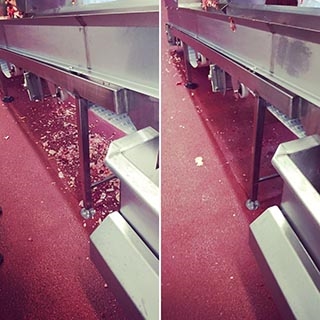 |
Pictured here is product carryback in a meat processing facility. The first photo is while using a homemade belt cleaner, the second photo is after installing an engineered solution on the conveyor system. |
Another option is to buy a cleaner specifically engineered to work with light-duty belting in food, pharmaceutical, or recycling applications. Most engineered cleaners have been field tested and proven to be gentle to your belting, but tough enough to remove even the stickiest of materials.
The effectiveness of engineered belt cleaners is evident from the moment they are placed on the system. They contain tensioning mechanisms for optimal interaction between the cleaning blade and the belt instead of relying on a fixed blade, as is often the case with homemade cleaners.
In fact, some operations have noted as much as a 60% reduction in scrap off the line when using an engineered cleaner rather than a homemade cleaner. For example, a meat packing operation was able to cut their waste by 70% after installing engineered belt cleaners.
They were experiencing large amounts of product loss on the return side of its conveyor since the product was sticking to the plastic modular belt and falling to the floor. The cost of the waste was estimated at $150 per shift. With two shifts per day, the estimated cost of carryback was $300.
By installing an engineered belt cleaner, they reduced the waste on their belt line by 70-80%, translating to a reduction of $210-$240 dollars of waste per day. With a line that runs five days a week, those savings will add up to a reduction in lost product of $54,600 to $62,400 per year. In addition, the facility does not have to clean up the carryback that was previously falling onto the floor. You can read more about this real life story here.
Engineered cleaners that are specific to the food or pharmaceutical industry are also made from food grade materials and are designed to ensure that cleaning and sanitizing is quick and easy. For extra peace of mind, food operations should seek out engineered cleaners that meet strict sanitary guidelines and are certified by the USDA for use in their industries. In some multinational food and pharmaceutical operations, a European Union certification may be required in order to have common engineered cleaners among facilities.
One option is the FGP Food Grade Precleaner. The FGP meets the highest standards for food processing. The cleaner is easy to install, easy to maintain, and disassembles in a snap for regular cleaning and sanitization. Its stainless steel components and food grade materials limit crevices and opportunities for bacteria growth.
The Most Effective Solution
If you are struggling with carryback in your facility, the evidence is clear that an engineered belt cleaner is your best defense. You’ll decrease your product waste and the time spent maintaining and cleaning up your system, and most importantly, you’ll increase your belt life, your productivity, and your profits. Invest in the right technology, and you’ll have a great solution to add to your playbook.
If you’re interested in reading more real life stories from the field, here’s one food processing plant conveying sticky potato chip dough, another food processing plant conveying peas, lima beans, and corn, and one more food processing plant conveying frosted breakfast pastries.
Authored by: Ramses Banda Marquez, Product Manager
Banda Marquez manages the overall marketing strategy and activities associated with the light-duty mechanical fastener line and belt conveyor products. He brings expertise in marketing, product management, operations, engineering, and supply chain management to Flexco, along with extensive experience in distribution and international business. Banda Marquez also holds patents in both the U.S. and Australia. Banda Marquez earned a bachelor's degree in Mechanical Engineering from Baja California State University and a master's degree in Project Management from Keller Graduate School of Management.